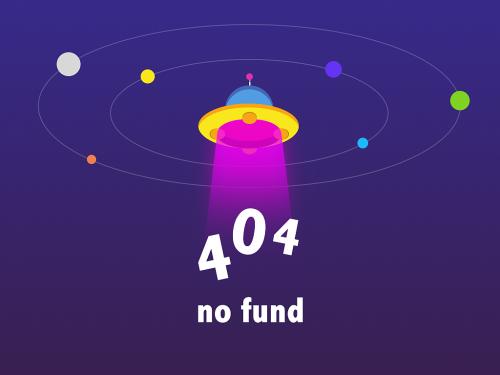
new energy-saving direct current submerged arc furnace
·overview of dc electric arc furnacedc arc is superior to ac arc in terms of stability and unidirectionality, which has great benefits for heat transfer in metallurgical processes. theoretical analysis points out that the use of direct current instead of alternating current is a major technological innovation measure. since the dc current has no zero-crossing problem, the arc stability is improved and the interference to the power grid is reduced. the method of using direct current to smelt metals in a dc electric arc furnace is basically the same as that of an ac electric arc furnace. however, since the anode heat on the charge side is high, the electrothermal change efficiency of the dc arc is high.using a controllable thyristor static converter as the dc electric arc furnace power supply, the ac power can be converted to dc. by changing the conduction angle of the thyristor, the melting current can be continuously and smoothly controlled, and the maximum current does not exceed the allowable value of the equipment . the use of a three-phase full-bridge rectifier circuit enables the rectifier transformer to have many simple winding designs and a solid and reliable structure. since the adjustment of the conduction angle of the thyristor can only take effect when the next thyristor is turned on, there is a certain time lag. therefore, it is necessary to connect a dc reactor dcl in series on the dc side so that when the arc voltage drops instantaneously (short-circuit), the dynamic short-circuit current will not instantly reach an impermissible value.·features:1. the plc control is highly automated, the heating speed is fast, and the production rhythm is stable and reliable.2. according to customer requirements, it can be set arbitrarily during the smelting process without stopping, realizing different control schemes of constant power, constant current, constant impedance, and constant voltage, which is convenient and quick.3. on-load voltage regulation, stepless current regulation. during the smelting process, the voltage level can be arbitrarily increased or decreased according to requirements without stopping the machine. the current is accurate to every 1 ampere, increasing or decreasing arbitrarily.4. the anode and cathode are arbitrarily switched to change the polarity during the smelting process, and the furnace temperature is uniform, which effectively solves the defect of uneven temperature in the furnace caused by the anode effect. (this item is a patent)5. during the smelting process, the arc length can be adjusted arbitrarily according to the needs without power failure. it can be submerged arc or open arc smelting, and can melt various materials to achieve 2 in 1 composite multi-function use (electric arc furnace submerged arc furnace).6. the dc power supply main control board (independent intellectual property rights) has a soft-start function to avoid the phenomenon that the electrical components of the thyristor are destroyed by a high-voltage shock at a startup. the board has a photoelectric isolation function, which can effectively avoid the strong magnetic field at the production site from interfering with the stability of the control circuit during the production process. the board also has overvoltage, overcurrent, phase loss, and high temperature protection functions, which can effectively avoid damage to the equipment caused by short circuits.7. the electrode center temperature of dc electric furnace is high, the heat is concentrated, it is easy to bury the electrode deeply, the furnace bottom is not easy to rise, and it is more suitable for smelting products with high melting point.8. compared with ac electric arc furnace, dc electric arc furnace saves 1 to 2 sets of electrode devices, and graphite electrode consumption can be saved by 30%-50%. a 20t ac electric arc furnace requires about 6kg of graphite electrodes to melt 1t of molten iron, and a dc electric arc furnace of the same capacity only needs 3kg of graphite electrodes.9. it has the function of detecting broken electrode and automatically adjusting balance. when the electrode hits the bottom of the furnace, the arc light will be generated and it will not continue to run, so as to avoid the accident of breaking the electrode due to the continued downward movement of the electrode.ac electric arc furnace electrode breaking accident site10. the arc light of the dc electric arc furnace emits heat in a vertical form at the center, the heat is evenly distributed, and the materials are evenly melted. the direct current arc light has a strong electromagnetic stirring effect on the molten metal, so that the material is melted without dead ends and the product recovery rate is high.11. the noise is 10-20 decibels lower than ac electric arc furnace.12. the furnace wall refractories have a long service life. the angle between the arc of the ac electric arc furnace and the graphite electrode is 45°, which is very easy to hit the furnace wall, thereby destroying the refractory material of the furnace wall. the included angle between the arc of the dc electric arc furnace and the graphite electrode is 12°, which will not hit the furnace wall, will not form hot spots on the furnace wall, and will not damage the furnace wall refractories.·the principle of 10%-15% energy saving than ac electric arc furnace (power factor, harmonics, eddy current, skin effect):1. ac short network is easy to produce skin effect and proximity effect. it is difficult to maintain the balance of three-phase power, which leads to the increase of the useless power of the ac furnace. if high and low end compensation are not added, the power factor of the furnace is only about 0.7 to 0.8, even if compensation is applied after the cost, the furnace power factor is only about 0.8 to 0.9. the dc electric arc furnace manufactured by our company does not require a reactive power compensation device, and the natural power factor is as high as 0.95 to 0.98.2. in the ac circuit, due to the existence of the alternating current, the alternating magnetic field in the short network loop will then generate eddy currents, which will cause the short network loop to heat up, thus wasting a part of energy. however, the short circuit in the dc circuit will only generate a stable magnetic field, without the existence of eddy currents, there will be no heat, and no eddy current loss will be wasted energy.3. from the characteristics of the alternating current curve, it is found that the alternating current changes from a sine wave to a cosine wave at 50 hz, and the voltage crosses zero 100 times per second, that is, there are 100 arc ignition, arc extinguishing, arc re-igniting, and arc extinguishing every second phenomenon, the strong voltage flicker problem causes ac arc light instability, harmonic distortion, voltage and current out of phase. at the same time, harmonic pollution is generated. the 2nd, 4th and even harmonics coexist with the 3rd, 5th, and 7th odd harmonics and severely exceed the national standard by 5%~27%, which makes voltage distortion more complicated. the dc voltage has the characteristic of zero point, no polarity change, but weak and strong flicker, so the dc arc is more stable than the ac arc. in terms of flicker intensity, it is only 20% of the ac furnace, and the impact on the power grid is much smaller than that of the ac furnace, and there is no odd harmonic interference of 3, 5, 7, 11, and 13 to the power grid.4. alternating current itself has a skin effect. the current distribution inside the conductor in an ac circuit is uneven, and the current is concentrated in the "skin" part of the conductor, that is to say, the current is concentrated in the thin layer on the outer surface of the conductor. the closer to the surface of the conductor, the greater the current density, and the actual current inside the conductor is smaller. . as a result, the resistance of the conductor increases, and the power loss also increases. the dc current has no skin effect, so the short-circuit loop can pass a larger current in the same cross-sectional area, with high power utilization and low consumption.
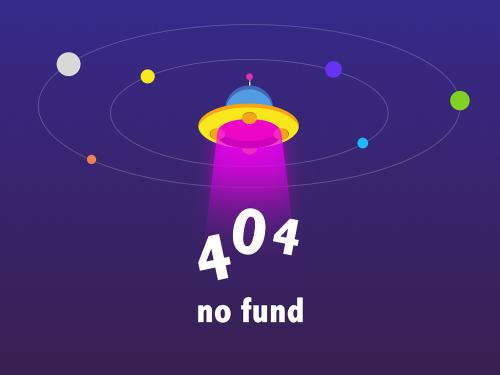
- inquiry hotline:
- address:northwest corner of the intersection of angang avenue and huaxiang road, anyang city, henan province
-
previous:100kⅴa dc experimental furnace
·overview of dc electric arc furnace
dc arc is superior to ac arc in terms of stability and unidirectionality, which has great benefits for heat transfer in metallurgical processes. theoretical analysis points out that the use of direct current instead of alternating current is a major technological innovation measure. since the dc current has no zero-crossing problem, the arc stability is improved and the interference to the power grid is reduced. the method of using direct current to smelt metals in a dc electric arc furnace is basically the same as that of an ac electric arc furnace. however, since the anode heat on the charge side is high, the electrothermal change efficiency of the dc arc is high.
using a controllable thyristor static converter as the dc electric arc furnace power supply, the ac power can be converted to dc. by changing the conduction angle of the thyristor, the melting current can be continuously and smoothly controlled, and the maximum current does not exceed the allowable value of the equipment . the use of a three-phase full-bridge rectifier circuit enables the rectifier transformer to have many simple winding designs and a solid and reliable structure. since the adjustment of the conduction angle of the thyristor can only take effect when the next thyristor is turned on, there is a certain time lag. therefore, it is necessary to connect a dc reactor dcl in series on the dc side so that when the arc voltage drops instantaneously (short-circuit), the dynamic short-circuit current will not instantly reach an impermissible value.
·features:
1. the plc control is highly automated, the heating speed is fast, and the production rhythm is stable and reliable.
2. according to customer requirements, it can be set arbitrarily during the smelting process without stopping, realizing different control schemes of constant power, constant current, constant impedance, and constant voltage, which is convenient and quick.
3. on-load voltage regulation, stepless current regulation. during the smelting process, the voltage level can be arbitrarily increased or decreased according to requirements without stopping the machine. the current is accurate to every 1 ampere, increasing or decreasing arbitrarily.
4. the anode and cathode are arbitrarily switched to change the polarity during the smelting process, and the furnace temperature is uniform, which effectively solves the defect of uneven temperature in the furnace caused by the anode effect. (this item is a patent)
5. during the smelting process, the arc length can be adjusted arbitrarily according to the needs without power failure. it can be submerged arc or open arc smelting, and can melt various materials to achieve 2 in 1 composite multi-function use (electric arc furnace submerged arc furnace).
6. the dc power supply main control board (independent intellectual property rights) has a soft-start function to avoid the phenomenon that the electrical components of the thyristor are destroyed by a high-voltage shock at a startup. the board has a photoelectric isolation function, which can effectively avoid the strong magnetic field at the production site from interfering with the stability of the control circuit during the production process. the board also has overvoltage, overcurrent, phase loss, and high temperature protection functions, which can effectively avoid damage to the equipment caused by short circuits.
7. the electrode center temperature of dc electric furnace is high, the heat is concentrated, it is easy to bury the electrode deeply, the furnace bottom is not easy to rise, and it is more suitable for smelting products with high melting point.
8. compared with ac electric arc furnace, dc electric arc furnace saves 1 to 2 sets of electrode devices, and graphite electrode consumption can be saved by 30%-50%. a 20t ac electric arc furnace requires about 6kg of graphite electrodes to melt 1t of molten iron, and a dc electric arc furnace of the same capacity only needs 3kg of graphite electrodes.
9. it has the function of detecting broken electrode and automatically adjusting balance. when the electrode hits the bottom of the furnace, the arc light will be generated and it will not continue to run, so as to avoid the accident of breaking the electrode due to the continued downward movement of the electrode.
ac electric arc furnace electrode breaking accident site
10. the arc light of the dc electric arc furnace emits heat in a vertical form at the center, the heat is evenly distributed, and the materials are evenly melted. the direct current arc light has a strong electromagnetic stirring effect on the molten metal, so that the material is melted without dead ends and the product recovery rate is high.
11. the noise is 10-20 decibels lower than ac electric arc furnace.
12. the furnace wall refractories have a long service life. the angle between the arc of the ac electric arc furnace and the graphite electrode is 45°, which is very easy to hit the furnace wall, thereby destroying the refractory material of the furnace wall. the included angle between the arc of the dc electric arc furnace and the graphite electrode is 12°, which will not hit the furnace wall, will not form hot spots on the furnace wall, and will not damage the furnace wall refractories.
·the principle of 10%-15% energy saving than ac electric arc furnace (power factor, harmonics, eddy current, skin effect):
1. ac short network is easy to produce skin effect and proximity effect. it is difficult to maintain the balance of three-phase power, which leads to the increase of the useless power of the ac furnace. if high and low end compensation are not added, the power factor of the furnace is only about 0.7 to 0.8, even if compensation is applied after the cost, the furnace power factor is only about 0.8 to 0.9. the dc electric arc furnace manufactured by our company does not require a reactive power compensation device, and the natural power factor is as high as 0.95 to 0.98.
2. in the ac circuit, due to the existence of the alternating current, the alternating magnetic field in the short network loop will then generate eddy currents, which will cause the short network loop to heat up, thus wasting a part of energy. however, the short circuit in the dc circuit will only generate a stable magnetic field, without the existence of eddy currents, there will be no heat, and no eddy current loss will be wasted energy.
3. from the characteristics of the alternating current curve, it is found that the alternating current changes from a sine wave to a cosine wave at 50 hz, and the voltage crosses zero 100 times per second, that is, there are 100 arc ignition, arc extinguishing, arc re-igniting, and arc extinguishing every second phenomenon, the strong voltage flicker problem causes ac arc light instability, harmonic distortion, voltage and current out of phase. at the same time, harmonic pollution is generated. the 2nd, 4th and even harmonics coexist with the 3rd, 5th, and 7th odd harmonics and severely exceed the national standard by 5%~27%, which makes voltage distortion more complicated. the dc voltage has the characteristic of zero point, no polarity change, but weak and strong flicker, so the dc arc is more stable than the ac arc. in terms of flicker intensity, it is only 20% of the ac furnace, and the impact on the power grid is much smaller than that of the ac furnace, and there is no odd harmonic interference of 3, 5, 7, 11, and 13 to the power grid.
4. alternating current itself has a skin effect. the current distribution inside the conductor in an ac circuit is uneven, and the current is concentrated in the "skin" part of the conductor, that is to say, the current is concentrated in the thin layer on the outer surface of the conductor. the closer to the surface of the conductor, the greater the current density, and the actual current inside the conductor is smaller. . as a result, the resistance of the conductor increases, and the power loss also increases. the dc current has no skin effect, so the short-circuit loop can pass a larger current in the same cross-sectional area, with high power utilization and low consumption.